Don’t Let Jitter Shake Up Your Flyback Converter Designs
Resonant ringing on
the transformer primary can be the cause of harmless variation in the
flyback converter’s duty cycle. However, if this side affect
is not properly identified early in the design process, it may be
misinterpreted as instability and lead to unnecessary and
performance-degrading redesigns.
By John Bottrill,
Senior Applications Engineer, Texas Instruments, Dallas
One of the more popular
topologies for startup and housekeeping power converters is the
discontinuous-mode flyback converter with peak current-mode control.
This topology is a favorite for converters producing 150 watts and
below, because it enables small size, simplicity, and minimal
magnetic components. Using the discontinuous, current-mode-contol
configuration allows the flyback topology to have a simple and
reliable feedback loop. A typical
circuit for this type of application is presented in the schematic in
Figure 1.

Figure
1. Basic discontinuous-mode flyback housekeeping power converter
One of the issues that
arises in the design of this converter is a variation in on-time
(jitter) due to ringing on the transformer primary. If that jitter is
erroneously attributed to instability, the designer may waste
precious development time “correcting” the converter
design. In some cases, the fix may even degrade converter efficiency.
Fortunately, some simple tests can identify the transformer ringing
as the source of the jitter. But before designers attempt to
diagnose the jitter, it’s important to understand its origins.
Modes of Operation
In the
discontinuous-mode, there are three states. All three occur within
the time when the internal timer is completing a single cycle. The
internal timer for the IC used in this example, a UCC38C44,
is a saw tooth ramp generator.
The first phase of the
converter is initiated by turning on Q1, which starts at the same
time that the ramp on the RT/CT pin starts to charge. The current in
the primary winding of T1 starts to increase, resulting in a voltage
being developed across RIsense. When this voltage reaches a peak, set
by the feedback loop, the main switch is turned off and the inductive
energy now stored in the primary inductance causes the voltage on the
windings of T1 to reverse polarity.
This is the beginning
of the second phase. During this phase, the energy stored in the
primary is delivered to the load in the form of current. This current
will decrease linearly to zero.
When the current hits
zero, the circuit enters the third phase where the main switch is off
and the transformer is not delivering energy to the output. This is
characterized by a resonant ringing of the voltage across the primary
winding.
The three phases can be
easily seen in Figure 2, which shows both the voltage on Q1
and across RIsense.
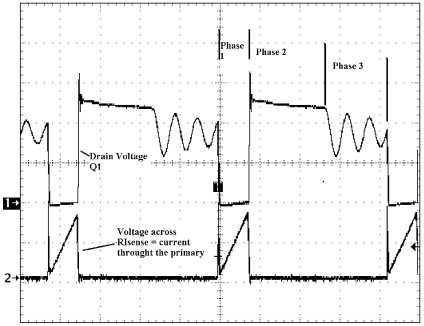
Figure
2. Typical discontinuous main switch voltage and primary current
A quick review of the
requirements for a discontinuous flyback may be in order. For a fixed
frequency converter operating at minimum input voltage and maximum
load, the total “ON” time of the main switch plus the
time needed to deliver energy to the load must be less than 100
percent of the available cycle time. To avoid having the power switch
voltage on the drain ring below ground when the diode stops
conducting at minimum input voltage, the reflected voltage on the
primary should be less than the minimum input voltage.
For a fixed load,
primary inductance and frequency, the energy stored per cycle (hence
the output load) is a function of the peak current, so the
energy/power transferred to the transformer is:
(Formula 1)
The rate of the
current’s change in the inductor’s primary is fixed for a
fixed input voltage and primary (magnetizing) inductance:
(Formula
2)
In a stable circuit with a fixed input and output voltage, load and
operating frequency, there should be a fixed and stable “ON”
time to achieve a specific energy transfer. Parasitic components can
result in slight variations to this ideal condition. These can give
the appearance of instability in a stable circuit.
To understand this, you have to look at the effect of the circuit
when the switching occurs. In particular, look at the voltage across
the main switch and the current in the inductor immediately after the
output diode stops conducting and just before the power switch turns
on. A simplified view of this circuit is shown in Figure 3
where Lmag represents the primary side magnetizing inductance, Csum
the collective parasitic capacitance, and Rwinding the effective
winding resistance.
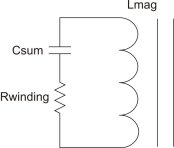
Figure 3. Simplified view of circuit at the start of
Phase 3.
At this point, the circuit is an L-R-C series resonant circuit (where
Csum is the sum of the total capacitances across the windings) that
is charged to the reflected output voltage with a dc offset equal to
the input voltage. The reflected output voltage is across Lmag. This
circuit will ring at a frequency set by the inductance, Lmag and the
capacitance, Csum according to Formula 3:
(Formula
3)
Since one terminal of the transformer is connected to the input
voltage, the circuit will have a dc offset equal to Vin. The waveform
will decay as a function of the losses represented by Rwinding. A
representative voltage and current waveform is shown in Figure 4.
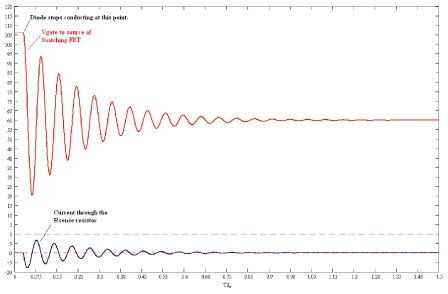
Figure 4. Representative voltage and current waveforms
for the ringing across the primary winding of the transformer
Figure 4 shows the voltage waveform on the drain of the
switching FET and primary winding current. These waveforms show the
end of Phase 2 and the beginning of Phase 3. The voltages, currents
and time in Figure 4 are representative and are not to scale.
If the time between the diode conducting and the main switch turning
on is long enough, the ringing dies out and there is no perceptible
jitter. However, if the time is short and significant ringing is
still present at the start of the next Phase 1, there may be jitter.
This is the case for the waveforms of Figure 2 and shown in
Figure 5.
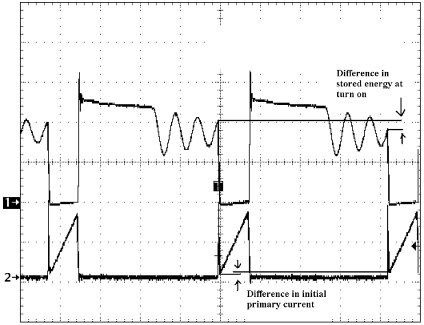
Figure 5. Different energy levels at the start of two
waveforms and the resulting current step.
The ringing represents the oscillating current and voltage within the
transformer’s primary winding. Ignoring losses and referring to Figure 3, the energy in the system is initially represented by
the maximum voltage across the capacitance. This energy will be
converted to current through the inductance over the resonant ring
cycle. This conversion results in the maximum current through the
winding according to the following equations where E is the total
energy in the system. At any point on the ring waveform (different Vs
and different Imags), the sum of the Formulas 4 – 5
(ignoring losses) should be E:
(Formula
4)
(Formula
5)
If V is the effective instantaneous voltage across the primary
winding at the point where the output diodes stop conducting, the
Imag is the effective current through the magnetizing inductance,
Lmag. When the voltage across the winding is ringing through the zero
point, the above formulas represent the maximum voltage and currents
within the closed circuit. Depending on the direction of the ring,
that current can be negative or positive.
So according to these formulas, depending on the point in the ring
cycle you will have different effective currents in the primary
winding. This results in different residual currents in the primary
winding. Thus, if the main switch turns on at different starting
points on the ring cycle, the circuit will have different starting
points on the current ramp. Since the starting point from
cycle-to-cycle can be different, the time to reach the same peak
current can be different, thus the “ON” time is
different.
The time when the converter’s main switch turns on is set by a
separate R/C oscillator as described earlier, so there is a fixed
time per cycle. The time to transfer the energy to the secondary is
fixed by the output voltage and the magnetizing inductance, which do
not change.
The remaining time now has a slight variation because of the slight
variation in the “ON” time, so now there will be a slight
variation in the ring time. This is shown in Figure 5 by the
point on the ring voltage waveform, where Phase 3 ends and Phase 1
begins. This results in the instantaneous current in the primary
having slight variations from cycle to cycle. This difference is
shown in Figure 5 by the difference in the initial voltage on
the current sense resistor at the beginning of Phase 1. It is this
behavior that leads to the variations in the “ON” time.
This variation in duty cycle can be misinterpreted as a stability
issue and result in extensive work to try to remove the problem. A
quick way to check this is to either increase or decrease the input
voltage. This will result in the ringing moving toward a peak or
valley when the main FET turns on as the input voltage changes. This
should result in a decrease in the amplitude of the jitter and, as
you get to the other side (down slope) of the waveform for the
transition, the effect tends to negate the jitter entirely as any
change results in less change on the next cycle.
Conclusion
Minimizing the parasitic capacitance limits the current in the
winding, increases the ring frequency and reduces the above described
effect, as the stored energy will be decreased. If you add damping
elements to minimize the ringing, this results in increased losses.
Since the jitter is not a result of instability and can be explained,
it should be safe to ignore it after recognizing the cause.
References
To download a datasheet
or other technical documents for the UCC38C44, visit:
www.ti.com/ucc38c44-ca.
For more information about power solutions from Texas Instruments,
visit: www.ti.com/power-ca.
About the Author
John Bottrill is a
Senior Applications Engineer at Texas Instruments, Manchester, NH.
John supports customers and evaluates new ICs before release. Through
this process, he has published multiple technical papers and has two
patents to his credit. He received his B. Sc. in Electrical
Engineering from Queen’s University at Kingston, Ontario,
Canada. You can reach John at ti_johnbottrill@list.ti.com.
For further reading on flyback converter design, see the How2Power Design Guide.
|